Création du planeur WOODY
Tuto et construction réalisés par Jean-Luc avec l’aide de Pascal Maurice pour la création du fuselage.
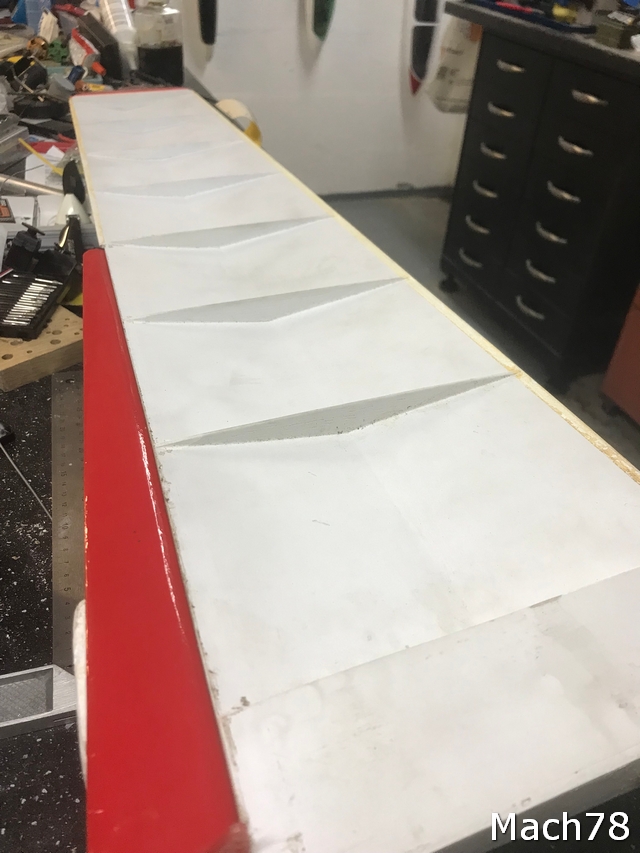
1/ Le profil de l’intrados.
- Ce modèle était vendu en trois envergures différentes: 2m – 2,5m – 3m
- Le fuselage d’origine, assez lourd, est en PLURA(tm) injecté à chaud. Cette matière plastique devient fragile dans le temps à cause des ultraviolets du soleil et malgré une mise en peinture tardive, il a subit des fissures dues aux chocs des atterrissages successifs qui ont fini par entraîner la destruction de la machine.
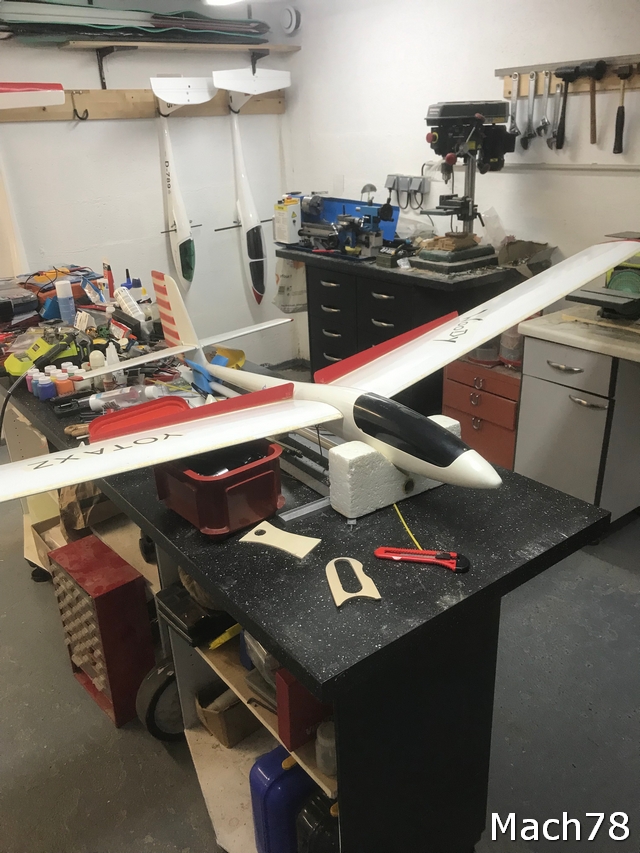
2/ Le WOODY de ROBBE assemblé dans l’atelier.
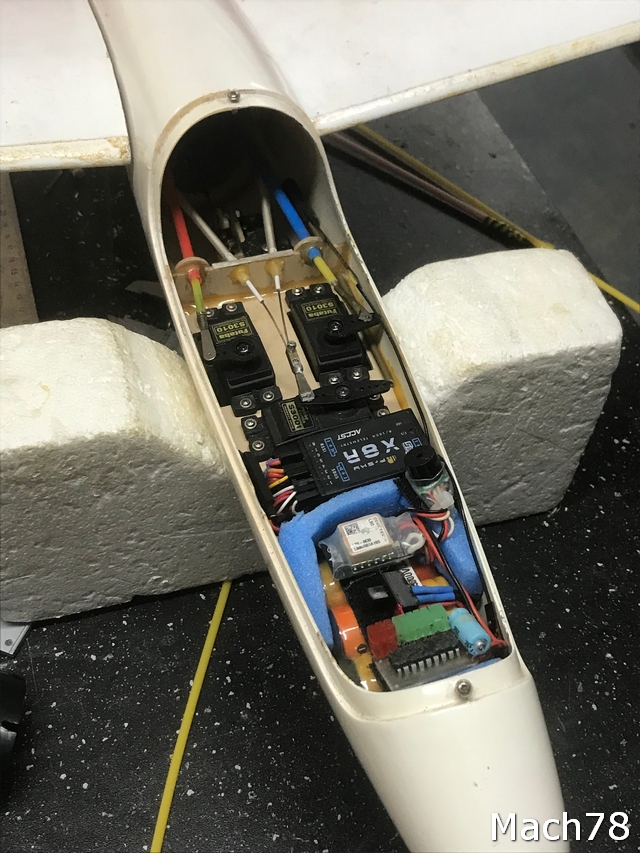
3/ L’installation radio sur le modèle original. On aperçoit le servo de direction (gaine rouge), celui de profondeur (gaine bleue) et le servo des volets de courbure en travers (gaines blanches). Un quatrième mini servo est dissimulé en arrière de la platine, il commande le crochet de remorquage situé dans le nez.
Après l’achat d’un deuxième fuselage, j’ai décidé de fabriquer un moule à partir de ce dernier, avant un nouvel assemblage du planeur neuf. N’étant pas plasturgiste et mes connaissances demeurant assez réduites en la matière, je me suis fait aidé par des semi-pro habitués à ce travail: Jacques DURDANT, et son fils William, de l’AMCL, ont réalisé le moule que voici en novembre 1994.
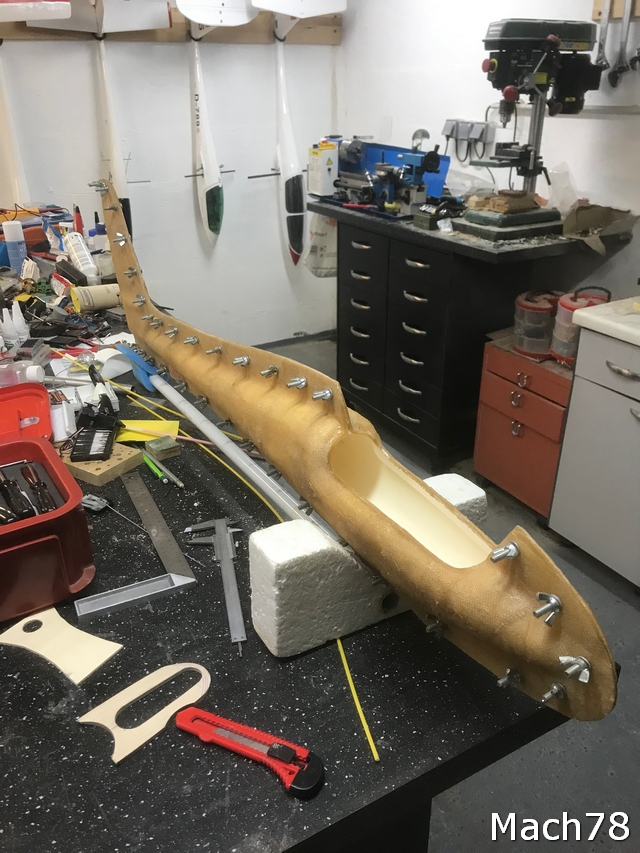
4/ Le moule assemblé
- Le temps a passé…
- Ce moule a “dormi” bien emballé pendant presque trente ans car je n’ai pas rencontré de plasturgiste capable d’en tirer une forme en fibre durant toute ces années.
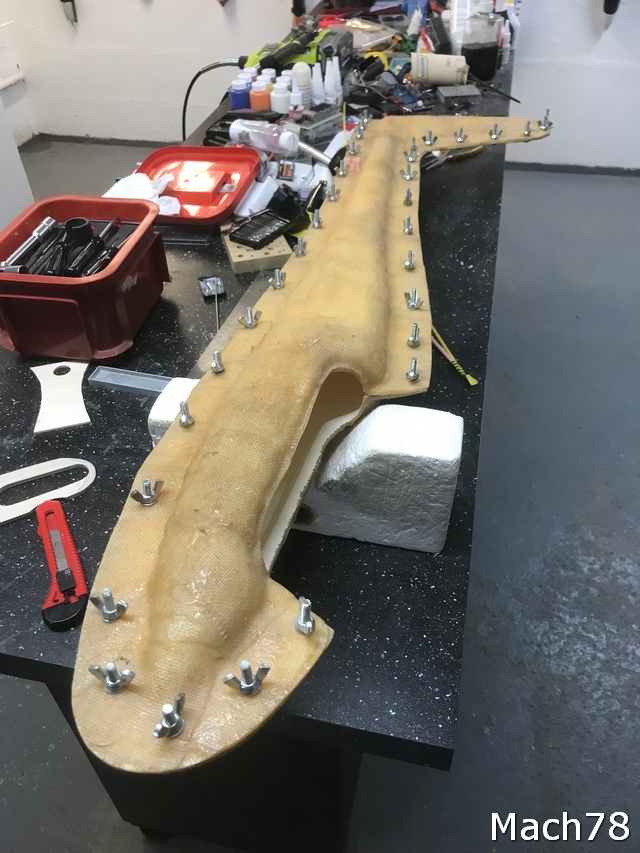
5/ Le moule assemblé
- En 2022, l’arrivée au MACH-78 de Pascal MAURICE, technicien confirmé, aguerri au travail des matériaux composites, a été l’occasion de voir si ce moule avait bien vieilli: pas de torsion, ni de vrillage et un bel état de surface.
- Pascal a donc réalisé plusieurs fuselages en résine et fibre polyester.
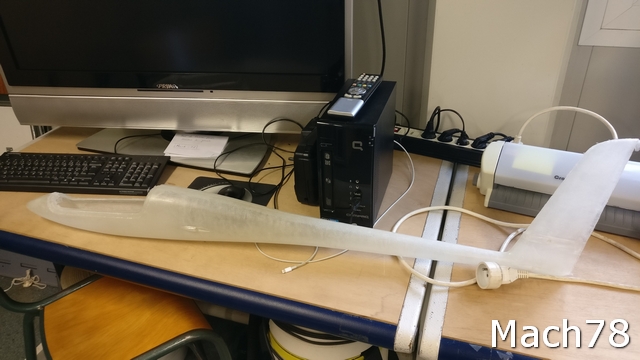
6/ Un fuselage brut de démoulage, sans gel-coat. Il sera peint ultérieurement.
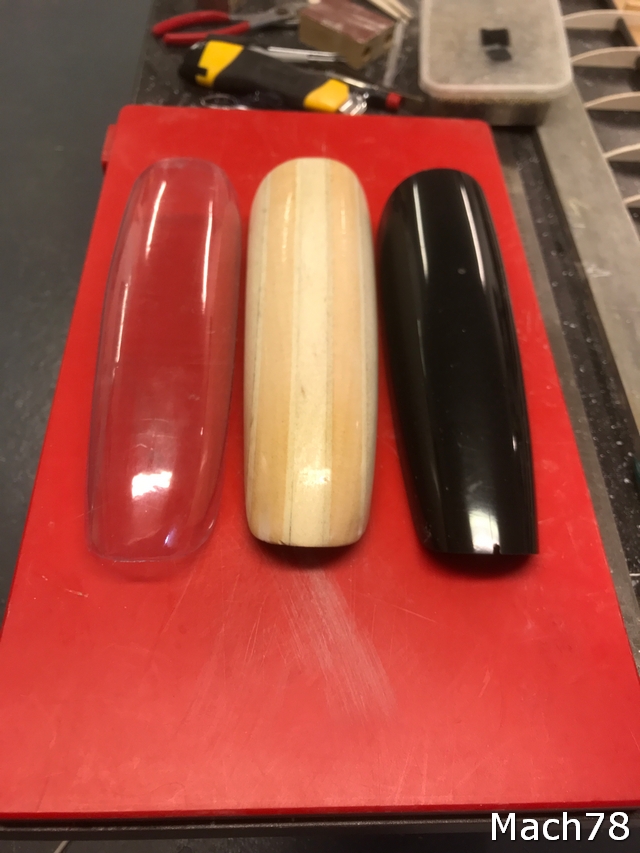
7/ La verrière finie et sa forme pour la thermo-rétraction.
- Les détails de la fabrication de celle-ci fait l’objet d’un tuto dans les pages du site du MACH-78, voir ici.
- A ce stade des travaux, je prends l’initiative de réaliser un futur planeur à propulsion électrique et de l’appeler REDFLAG.
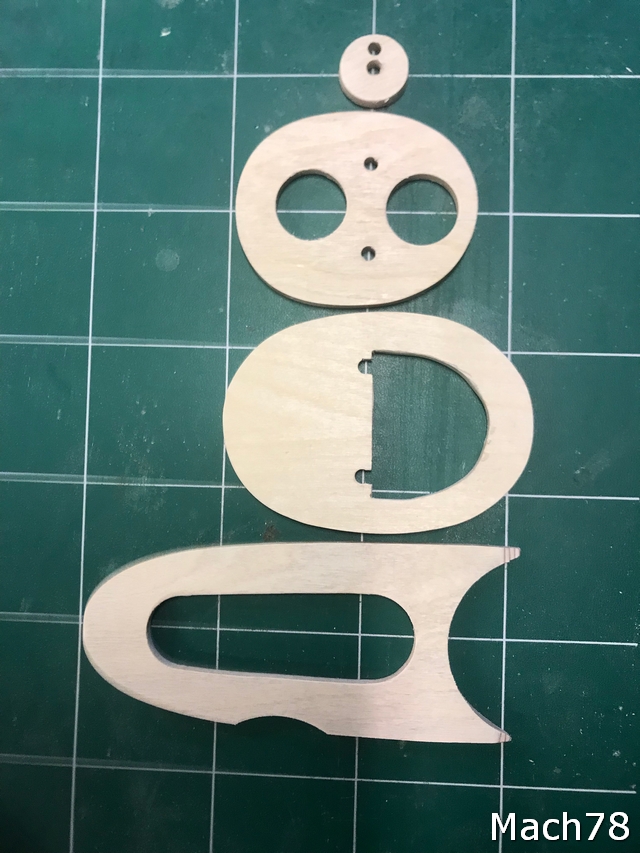
8/ Divers couples de renfort du fuselage en CTP de 5mm. En bas, la platine accus.
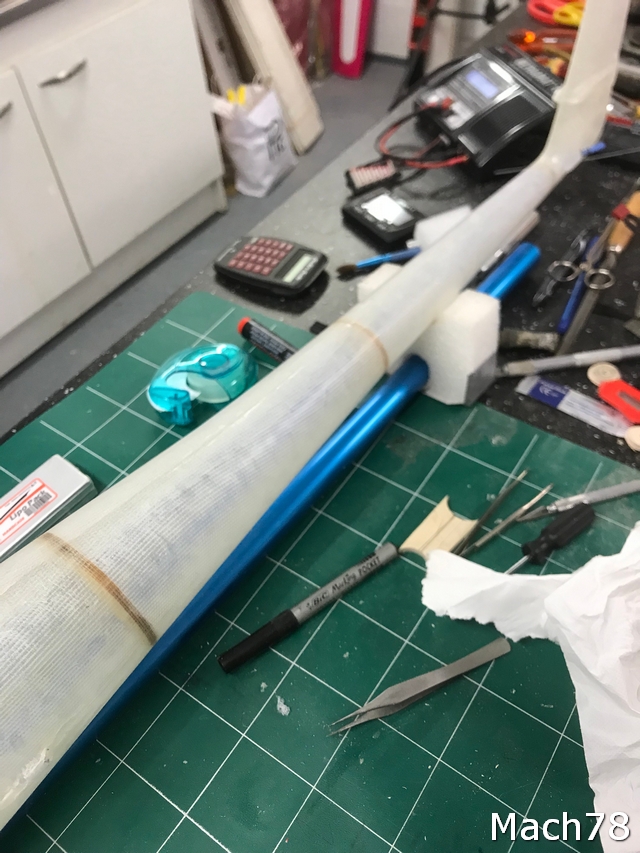
9/ Les couples collés en place.
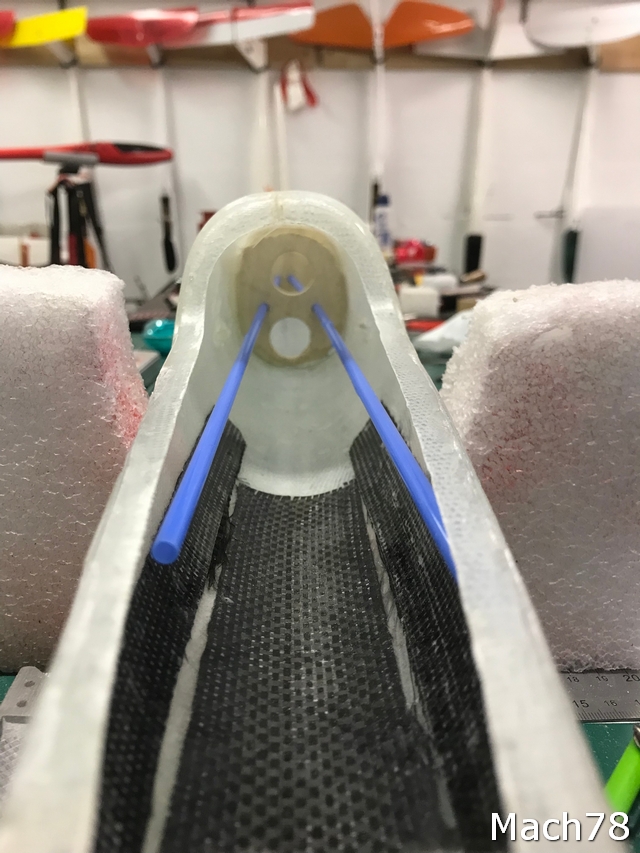
10/ Vue de l’intérieur du fuselage avec quelques bandes en tissu de carbone pour renforcer l’ouverture au niveau de la verrière.
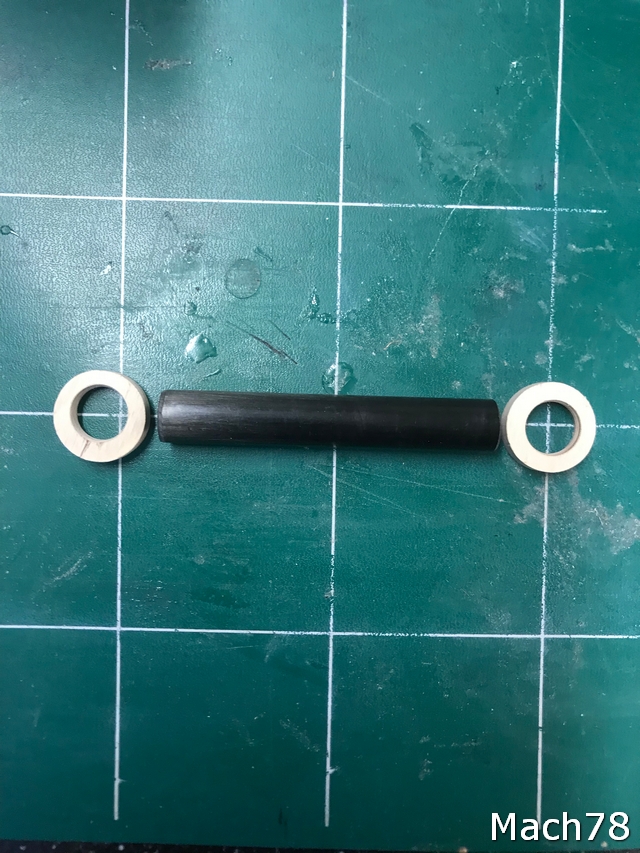
11/ Le fourreau de clé d’aile et ses renforts intérieurs pour une plus grande surface de contact lors du collage.
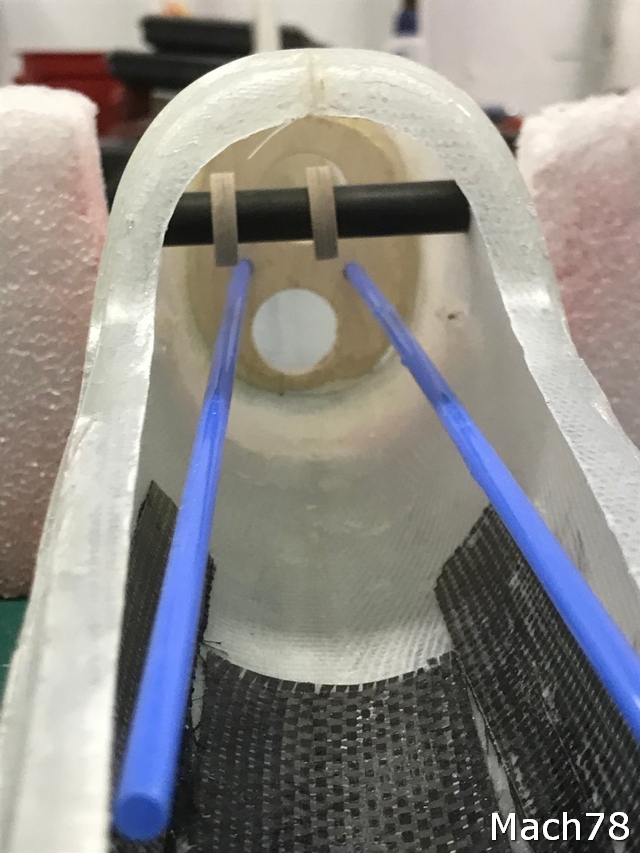
12/ Le fourreau en place avant collage.
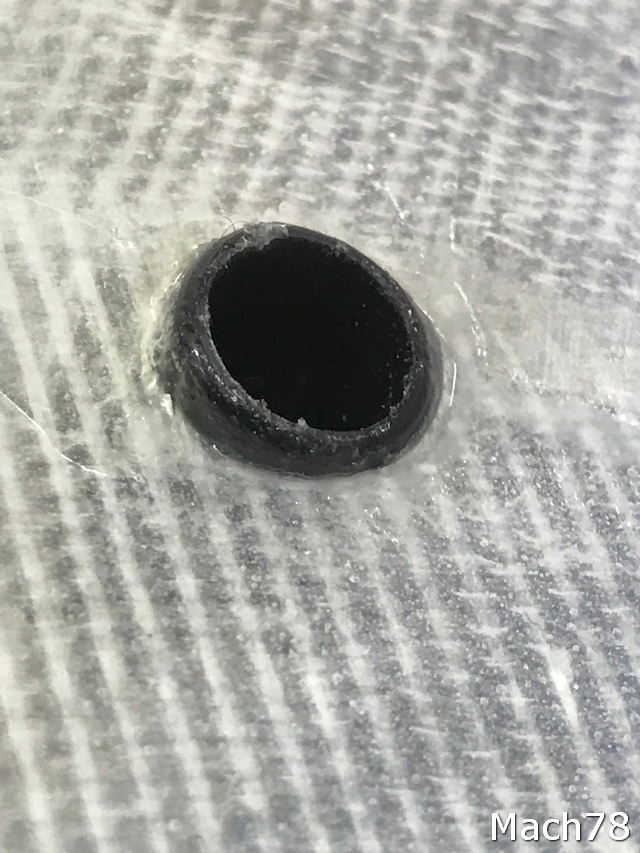
13/ Notez que celui-ci dépasse en longueur de 3mm de chaque côté du fuselage.
- Il est pointé à la cyano lente et épaisse par l’extérieur, puis collé à l’époxy 15mn par l’intérieur avec ses renforts. Il sera arrasé à la surface du fuselage ensuite.
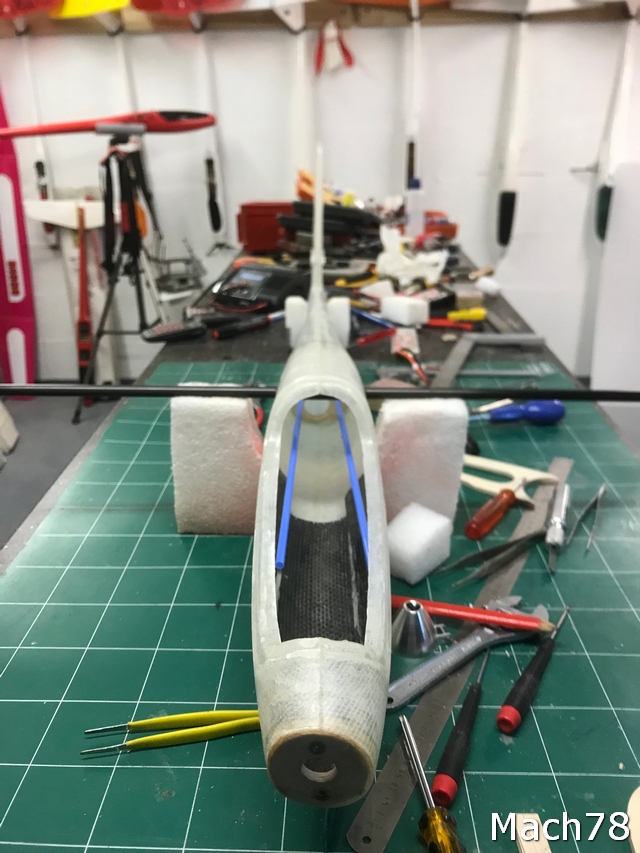
14/ Mise à l’équerre avant collage définitif du fourreau de clé d’aile.
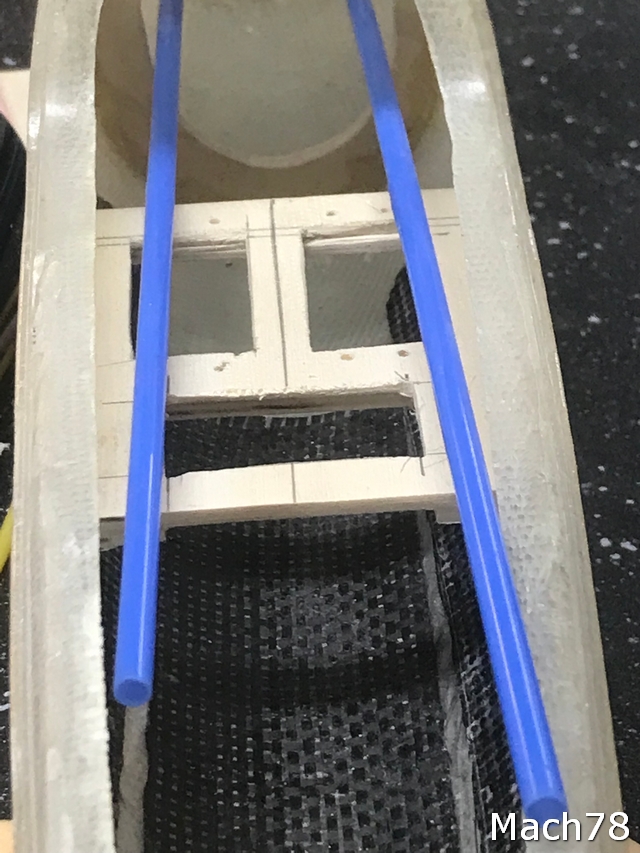
15/ La platine des servos – profondeur – direction – volets de courbure. Celle-ci a été reculée de 20mm par rapport au modèle original.
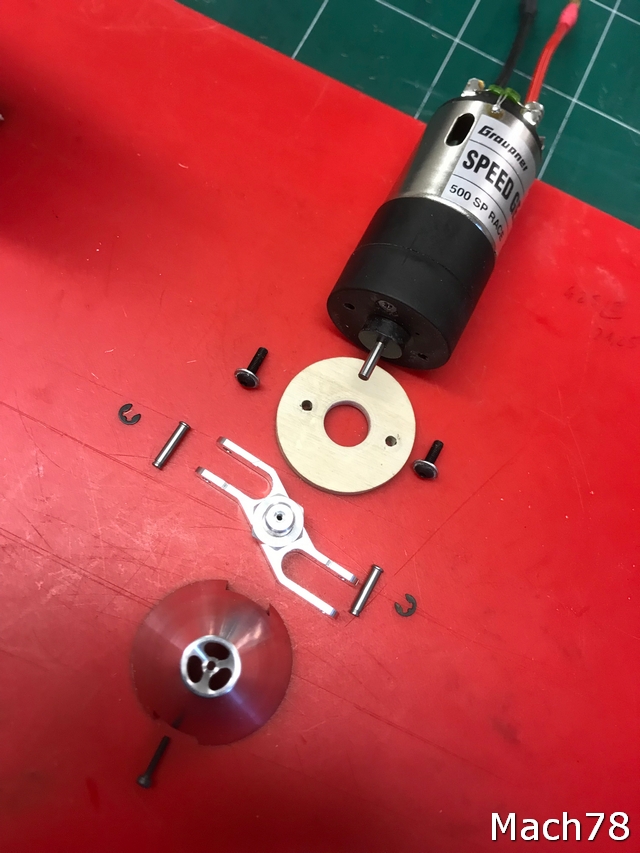
16/ Le moteur. C’est un SPEED SP 500 RACE brushed réducté 2,8:1, le cône, le montage d’hélice et le couple moteur.
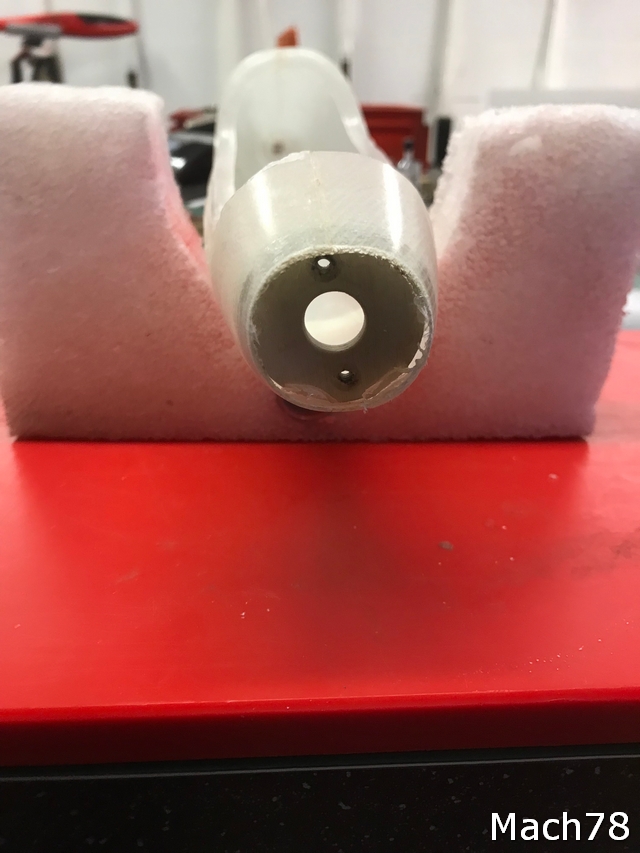
17/ Le couple moteur pointé en place à la cyano lente sans activateur.
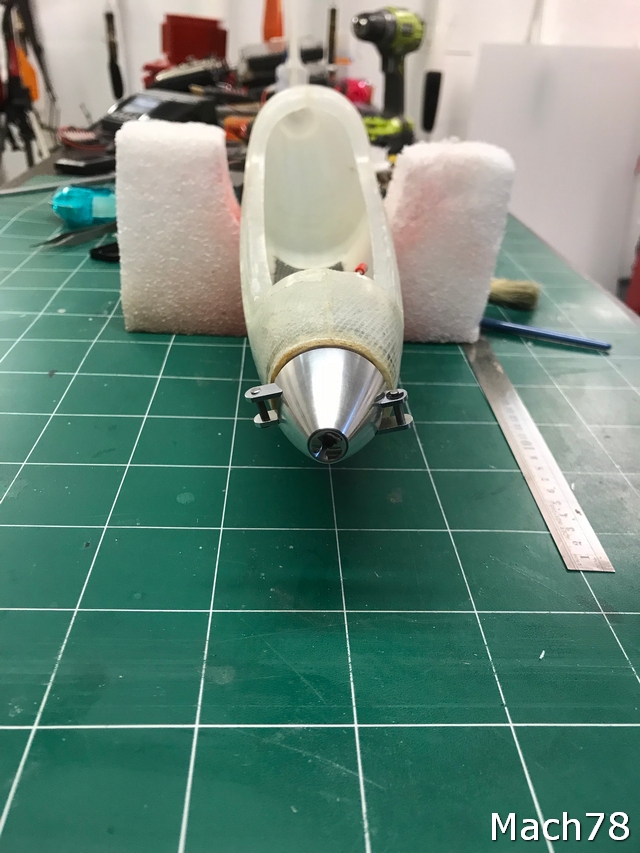
18/ Assemblage et mise au piqueur et à l’anticouple puis collage à l’époxy 5mn plus microballons par l’intérieur, en chauffant au sèche-cheveux pour rendre le mélange plus fluide et activer la polymérisation rapide une fois le couple bien positionné. (2°de piqueur et 3°d’anticouple)
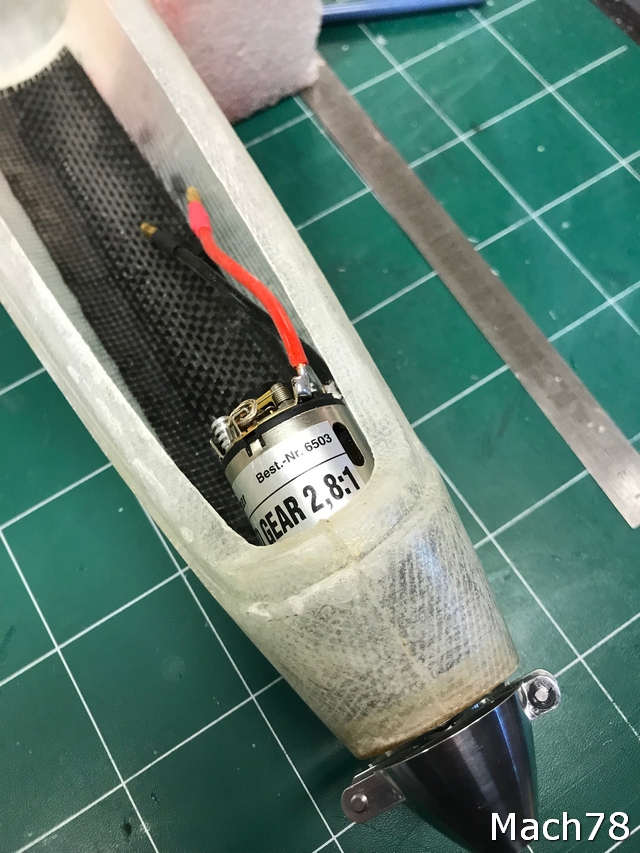
19/
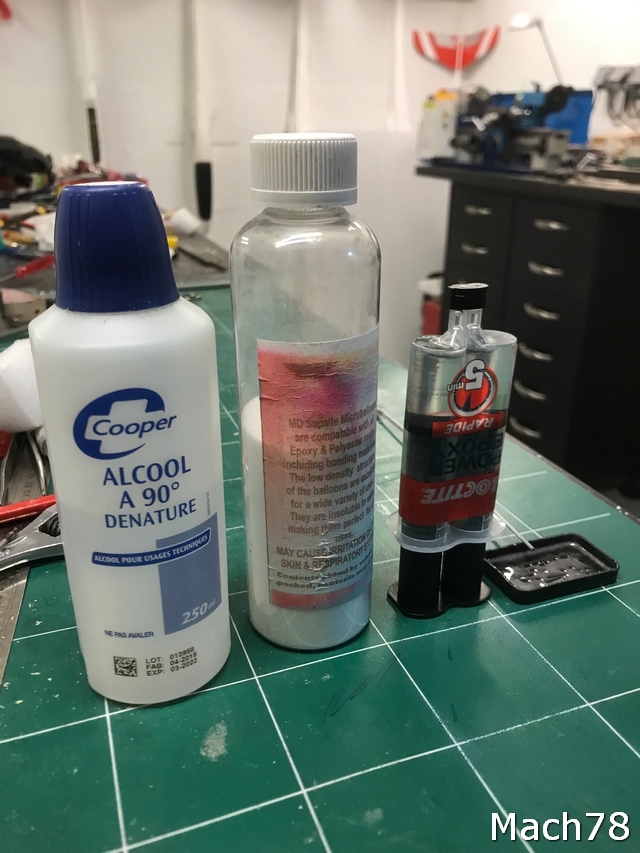
20/ Le trio gagnant: colle époxy 5 minutes, micro-ballons et alcool 90° pour plus de fluidité. (Deux gouttes suffisent)
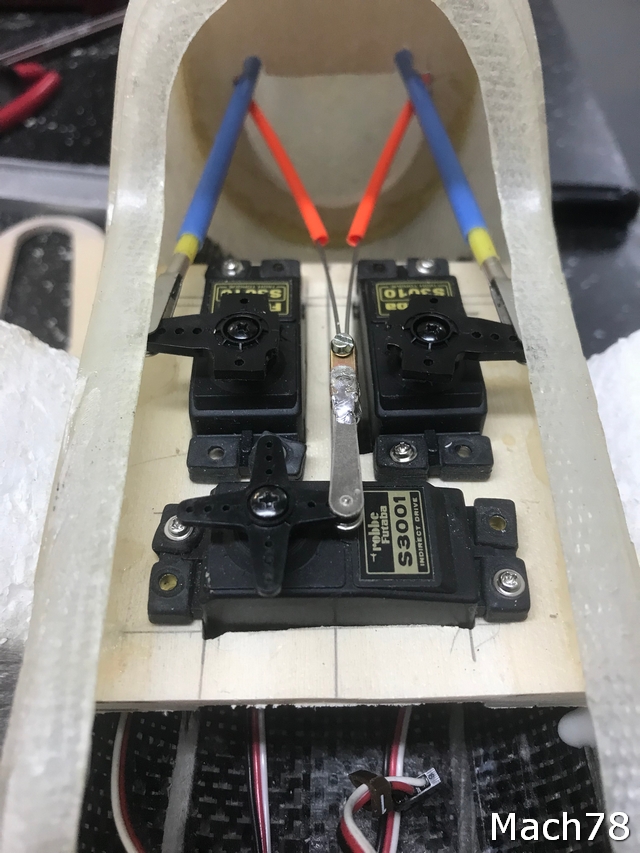
21/ Montage à blanc des servos pour dégrossir les débattements.
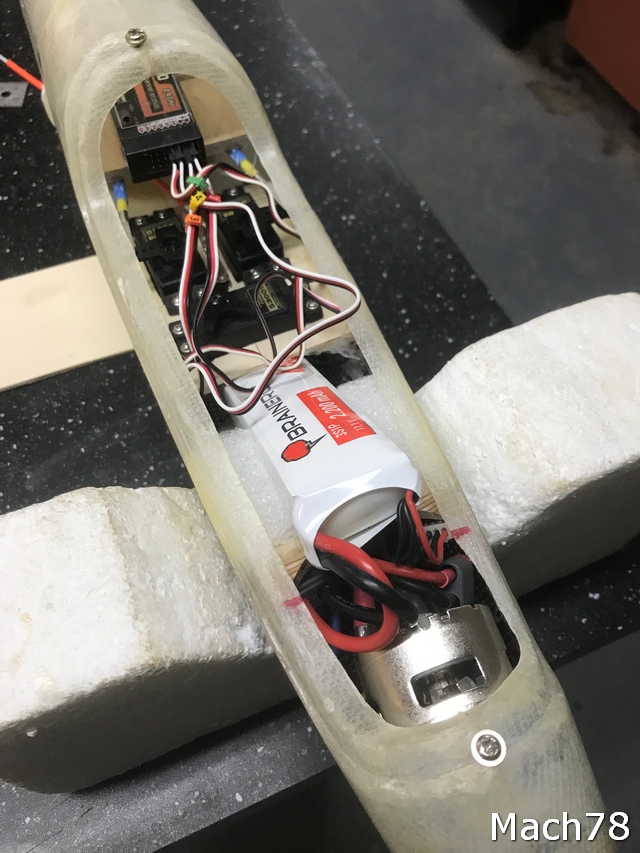
22/ Installation radio terminée avec l’accus 3s-2200mA et le moteur en place.
Notez que j’ai remplacé le moteur SPEED SP 500RACE réducté, trop long, par un SPEED RS 700BB en prise directe.
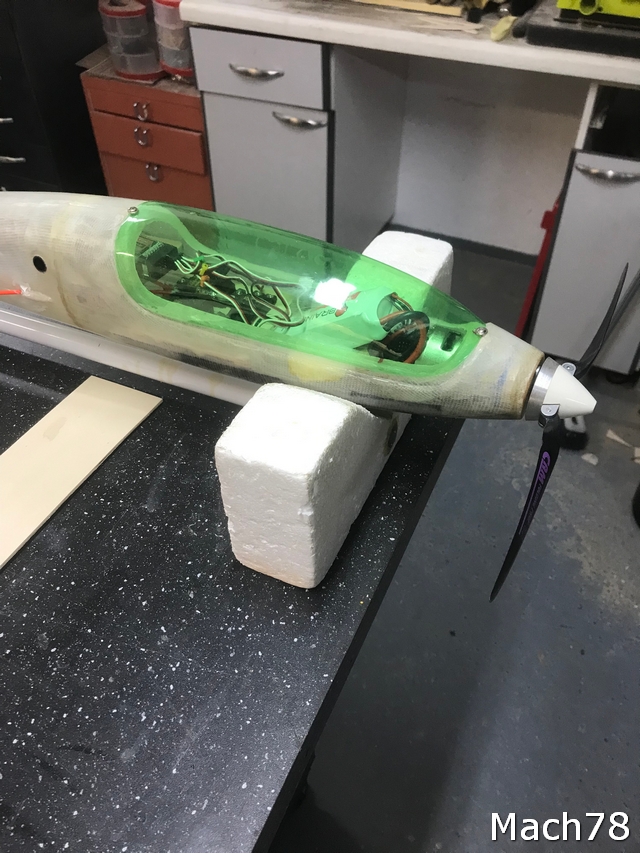
23/ Avec la canopée en place. L’hélice est une CAMPROP 12×6
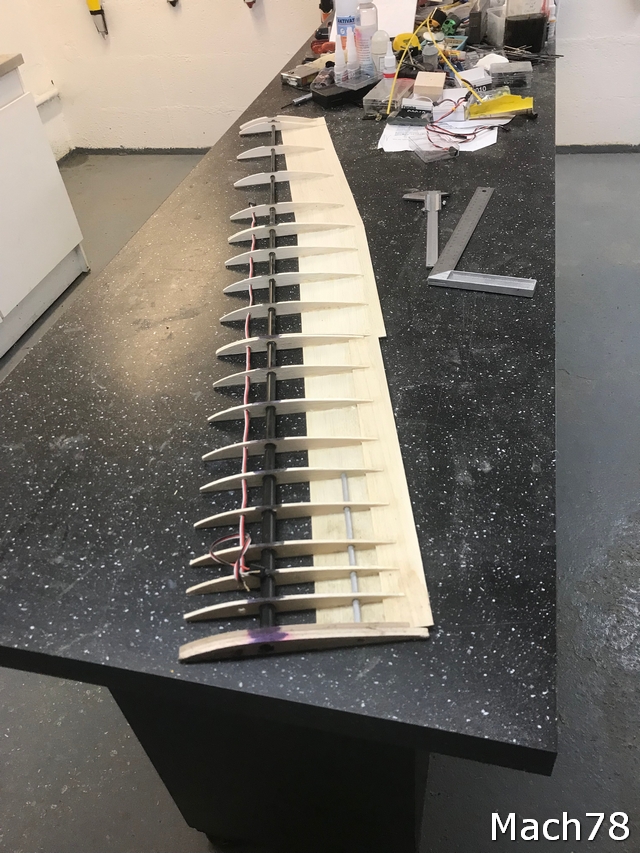
24/ Demie-aile en construction. Longeron en tube carbone dégressif, bord d’attaque en pin, tout le reste en balsa.
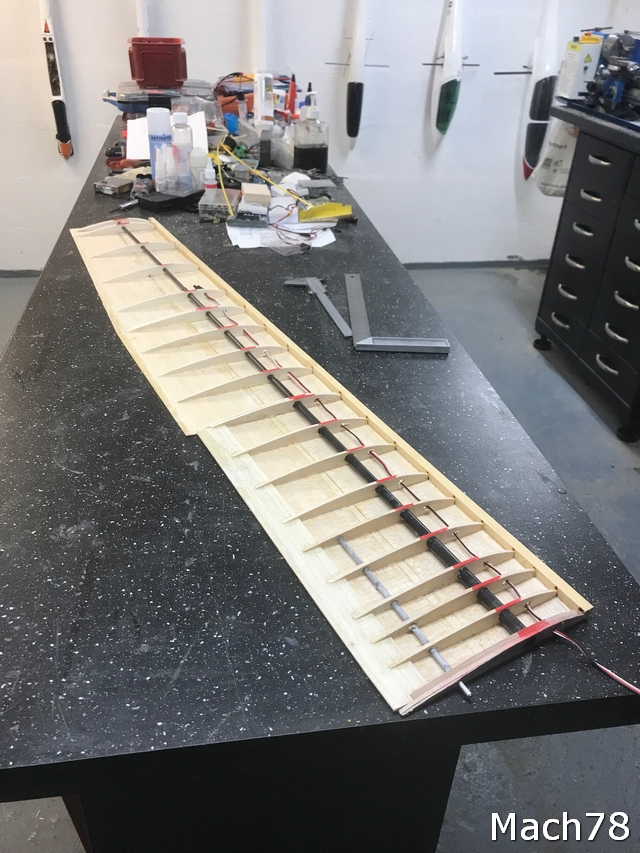
25/ Demie-aile avant coffrage complet de l’extrados. Le profil retenu est un CLARK-Z modifié (By courtesy of Professor Michael Selig)
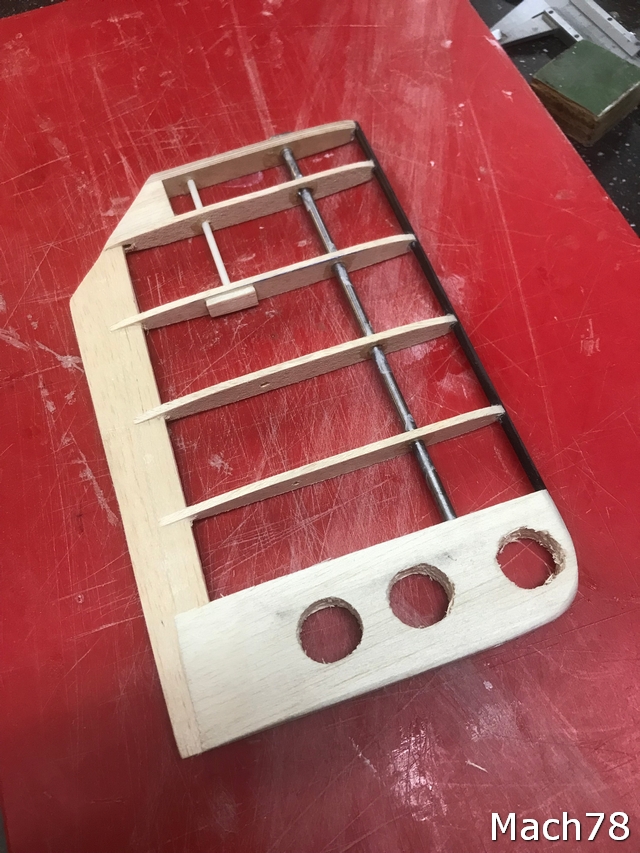
26/ Un demi-stabilisateur pendulaire terminé: le bord d’attaque est en tube carbone 4mm, le longeron en tube dural 5mm, nervures, bords de fuite et renforts en balsa 3mm.
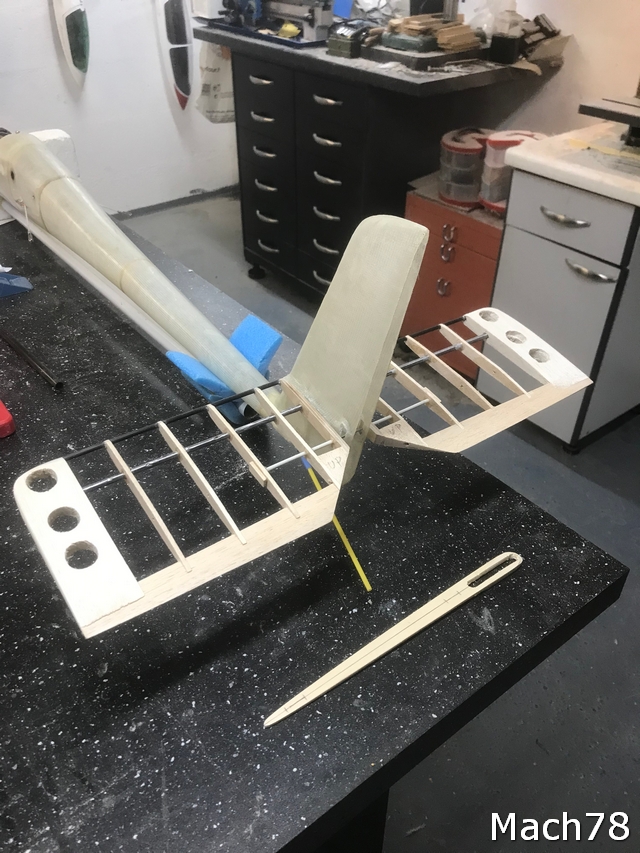
27/ Le stabilisateur complet en place. L’axe de rotation est un tube carbone de 4mm qui prends toute la longueur du longeron jusqu’aux saumons du stabilisateur. La commande de l’incidence est une corde à piano de 2,5mm légèrement cintrée à ses extrémités pour rentrer en force dans son tube. Sur le plan de travail, notez la baguette en CTP standard de 3mm qui fermera la dérive
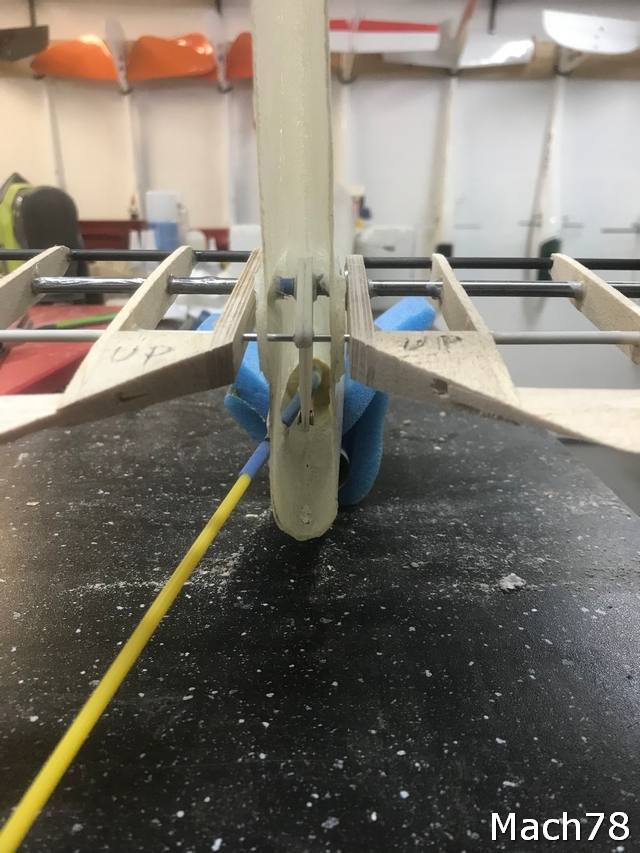
28/ Vue de la dérive avant fermeture. On aperçoit le renvoi d’angle en polycarbonate blanc. Celui-ci a été fabriqué à l’imprimante 3D par Pascal Maurice.
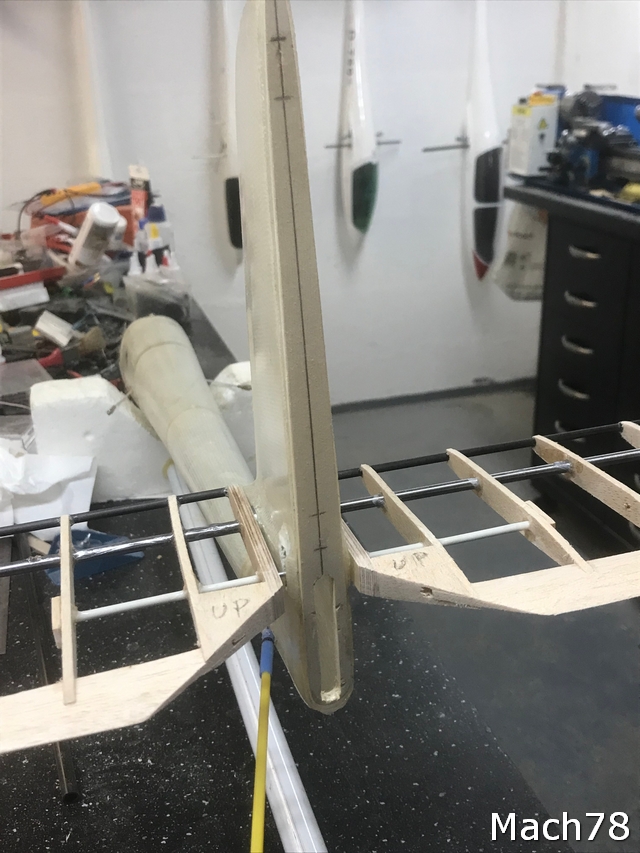
29/ La dérive fermée. La baguette CTP est pointée à la cyano-acrylate puis collée à l’époxy lente avec chauffe légère au sèche-cheveux. La boutonnière dans le pied de dérive sert de trappe de visite pour l’accès au renvoi d’angle.
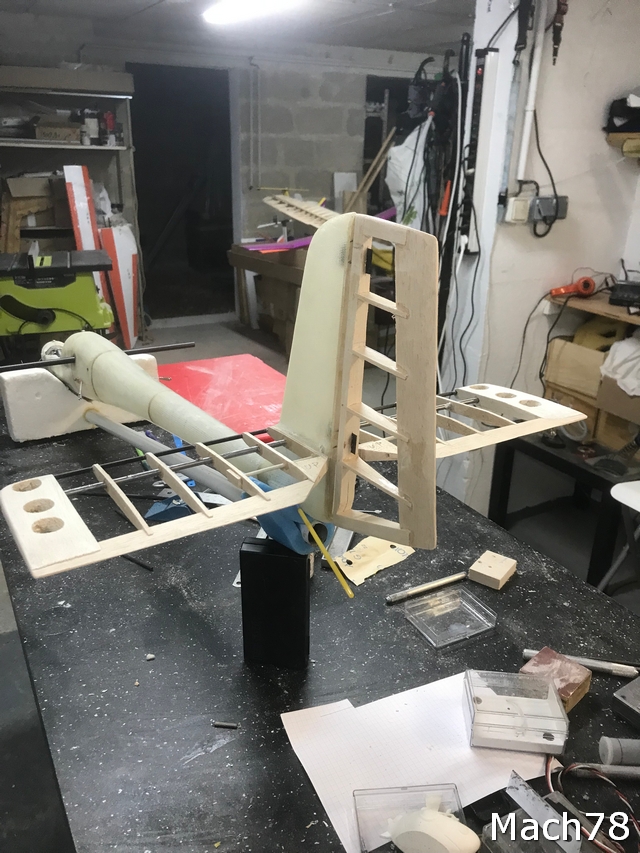
30/ Le stabilisateur et le volet de dérive en place avant l’entoilage. Les charnières de la dérive sont réalisées dans un morceau de vieille disquette informatique collée à la cyano lente pour une mise en place facile.
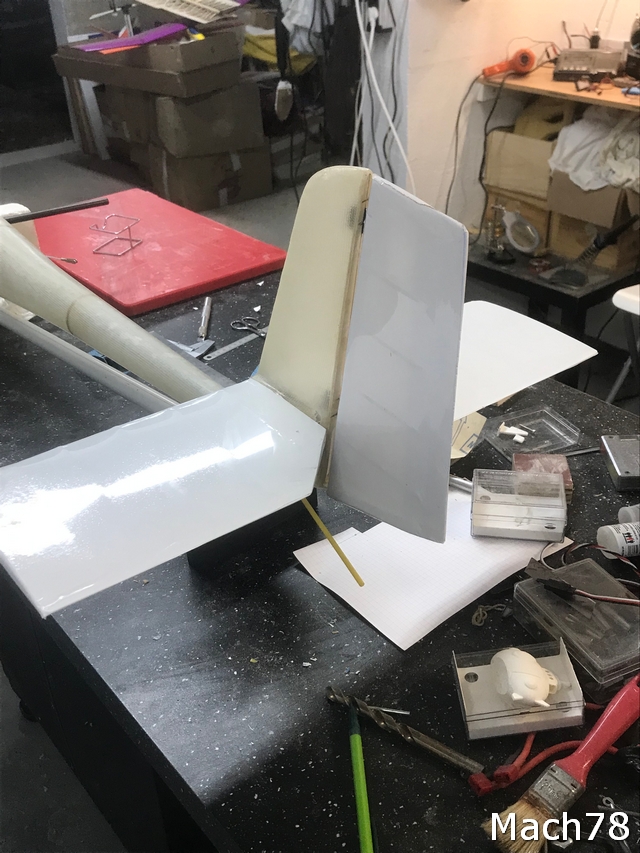
31/ Montage à blanc des gouvernes après entoilage. Pour la gouverne de direction, la charnière est verrouillée par un morceau de cure-dents en bois qui traverse le balsa et la disquette.
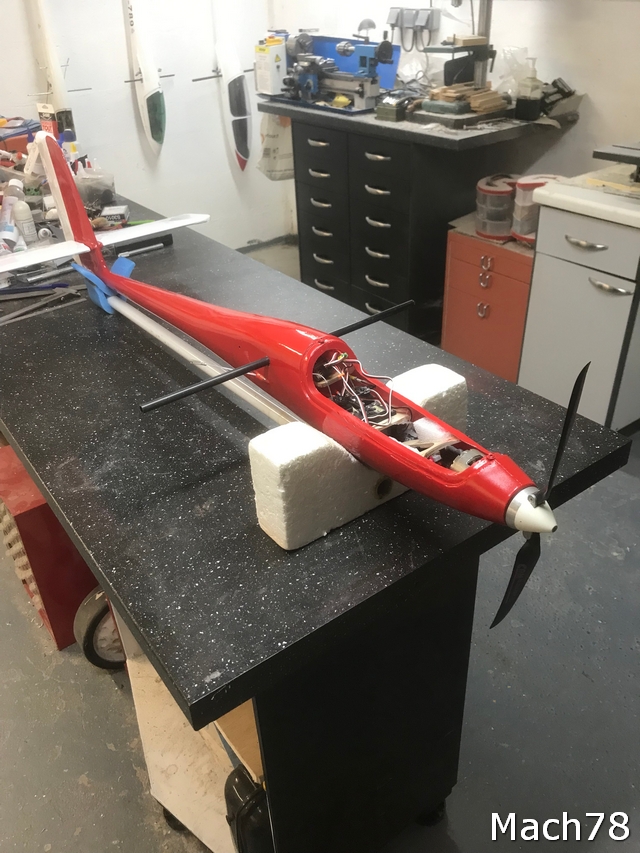
32/ Le fuselage du WOODY-REDFLAG après peinture.
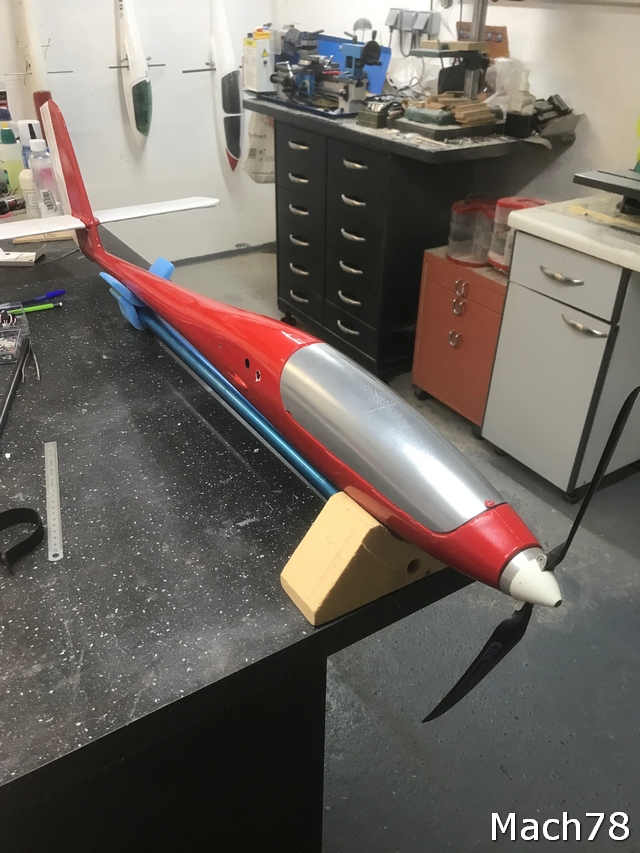
33/ Avec sa canopée en finition aluminium brillant.
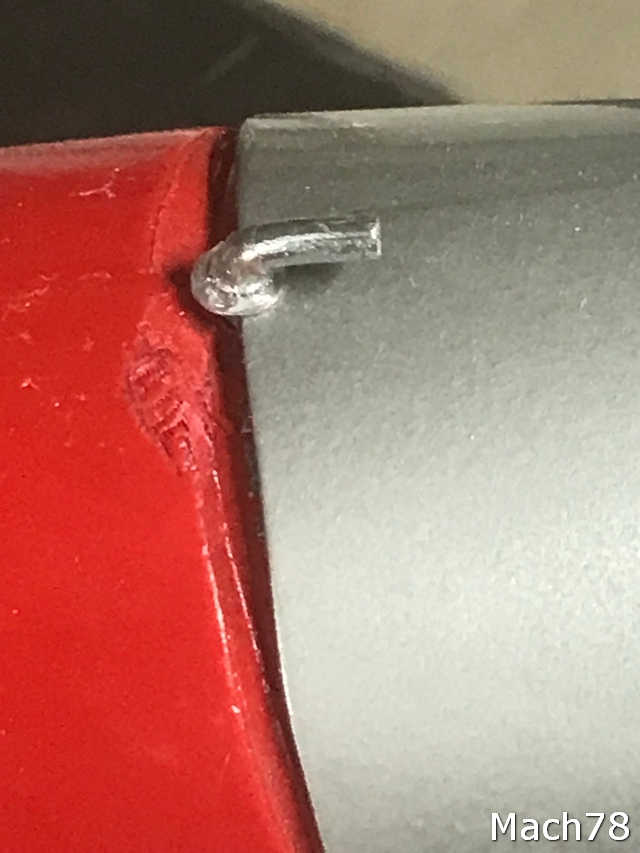
34/ Le verrou de canopée. C’est un clou plié à froid à 90° et actionné par un petit ressort de stylo dans le fuselage. Ce clou est fileté sur son extremité intérieure pour pouvoir visser un écrou de 3mm et ainsi bloquer le ressort qui fonctionne en compression. Le maintien de la canopée est assez ferme.
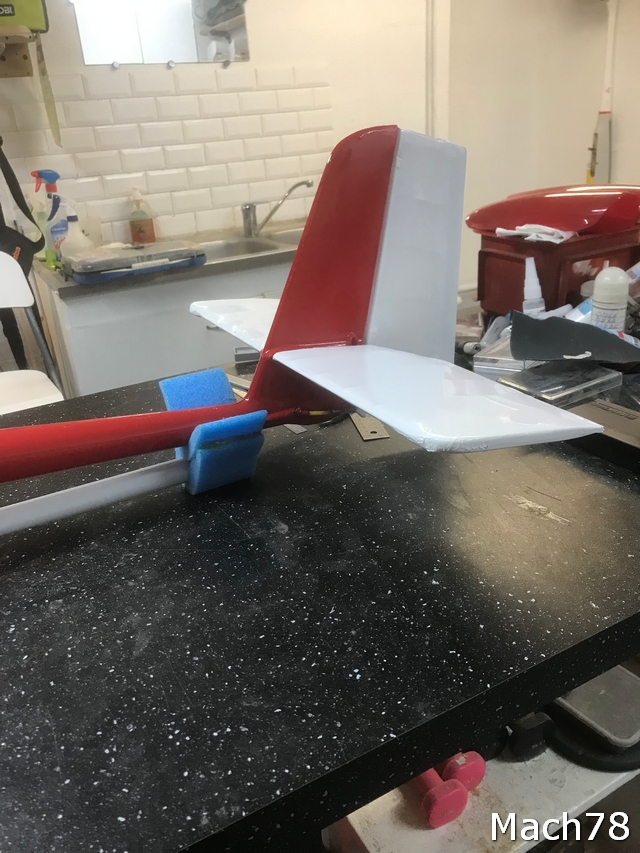
35/ Les gouvernes de profondeur et de direction calées au neutre avec les trims et sous-trims de la radio au neutre. (réglages par les fourchettes des palonniers des servos)
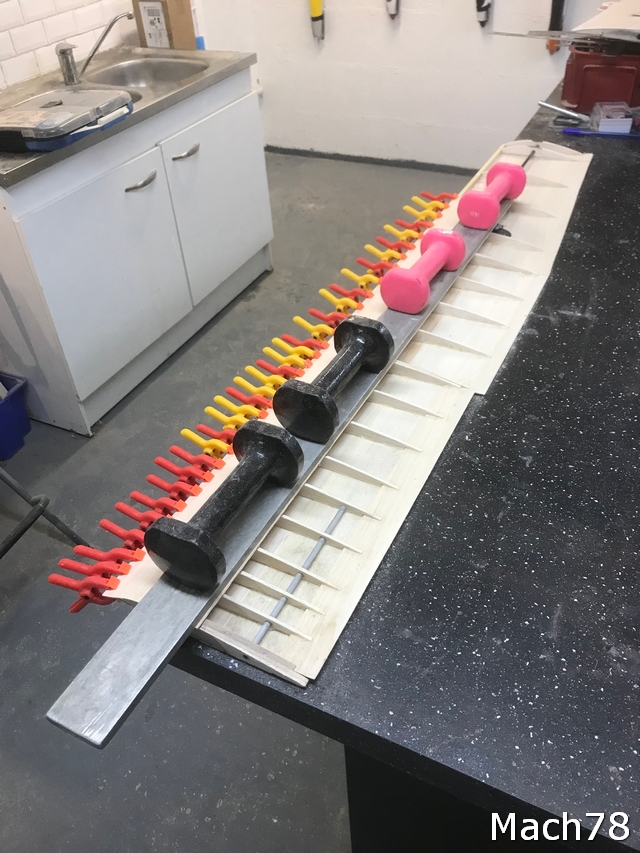
36/ Aile droite en cours de coffrage à l’extrados. Tous les collages bois sur bois se font à la colle à bois de qualité professionnelle (PATTEX).
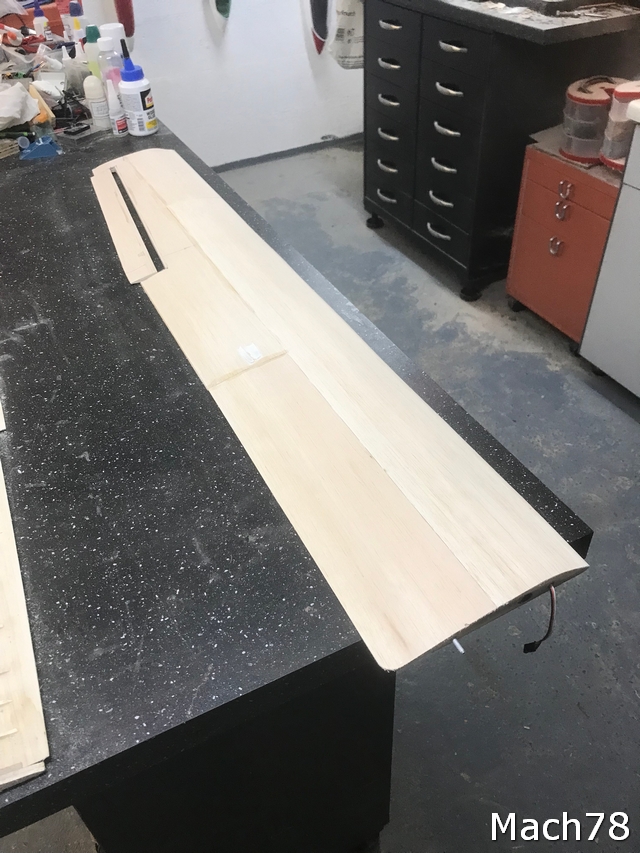
37/ Aile gauche terminée avec son aileron dégagé.
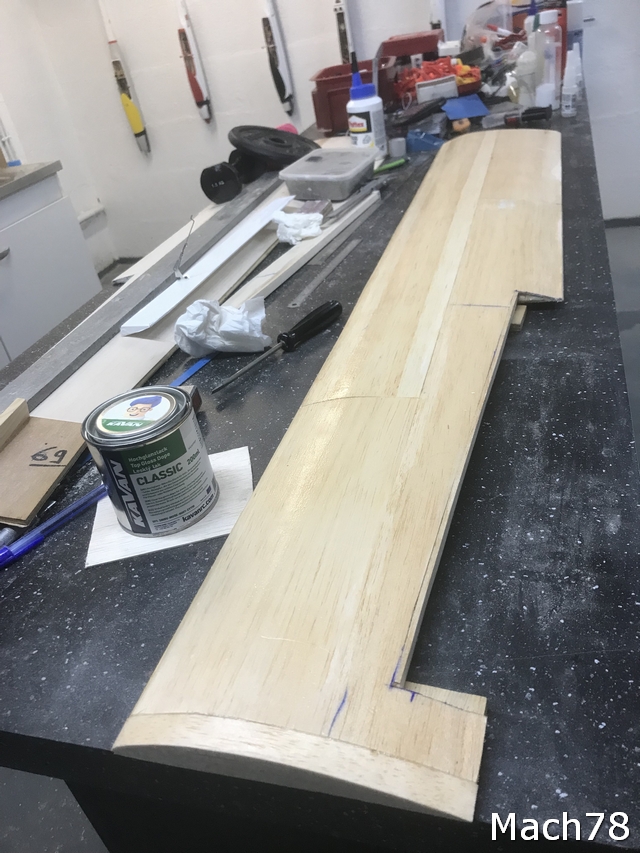
38/ Passage de l’enduit nitro-cellulosique (KAVAN classic vert) pour tenir les fibres du balsa: trois couches sur l’extrados (c’est IMPORTANT !) avec ponçage à sec au papier 240 entre chaque. Une seule couche sur l’intrados. Finition au papier 800 à sec sur l’extrados et l’intrados. La finition, surtout à l’extrados, doit être visuellement brillante et la plus lisse possible au toucher.
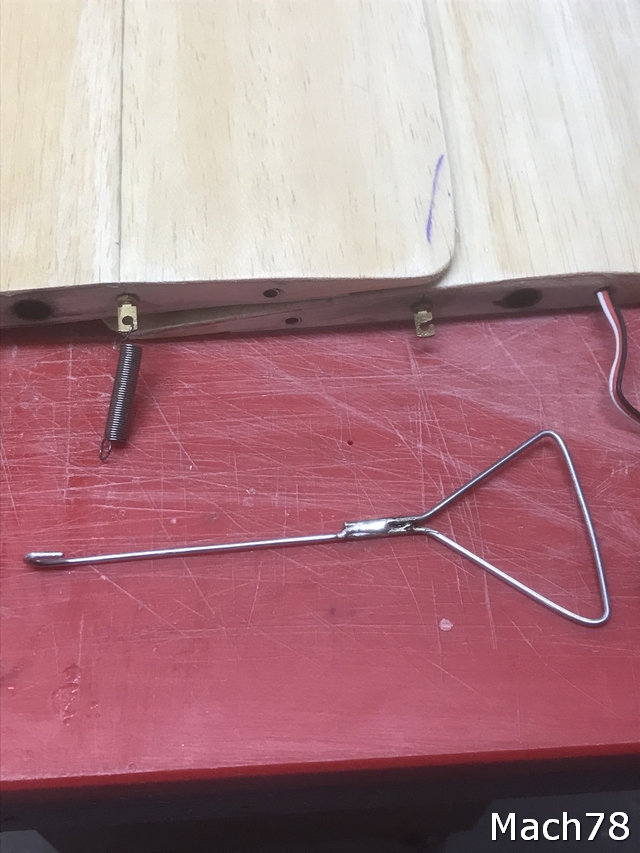
39/ Le système de verrouillage des demi-ailes sur la clé d’aile: deux attaches métalliques collées-vissées dans la nervure d’emplanture en CTP aviation de 5mm et un petit ressort costaud qui fonctionne en traction. En bas, l’outil-crochet qui sert à tirer le ressort à travers le fuselage. C’est un simple morceau de cintre métallique plié et soudé à l’étain.
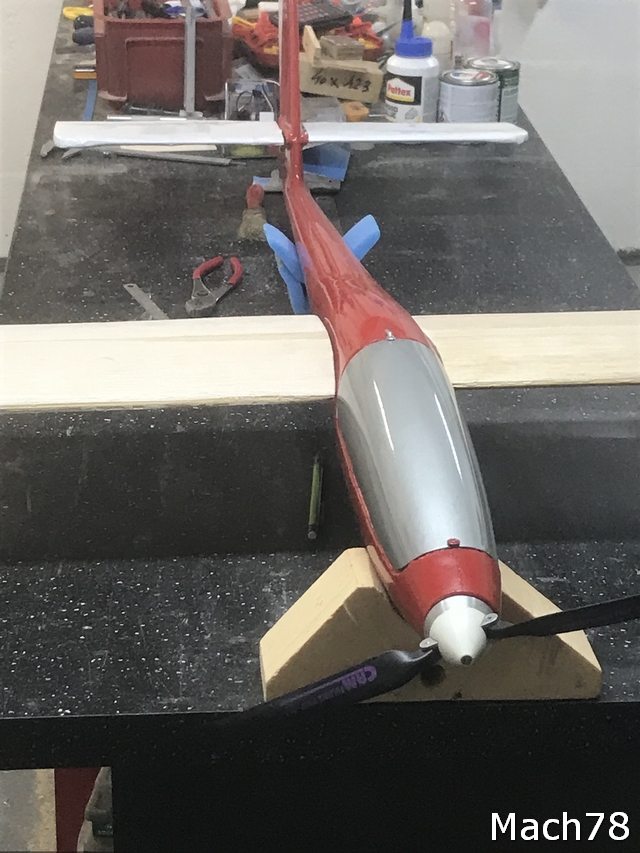
40/ Les ailes maintenues en place par le verrouillage du ressort.
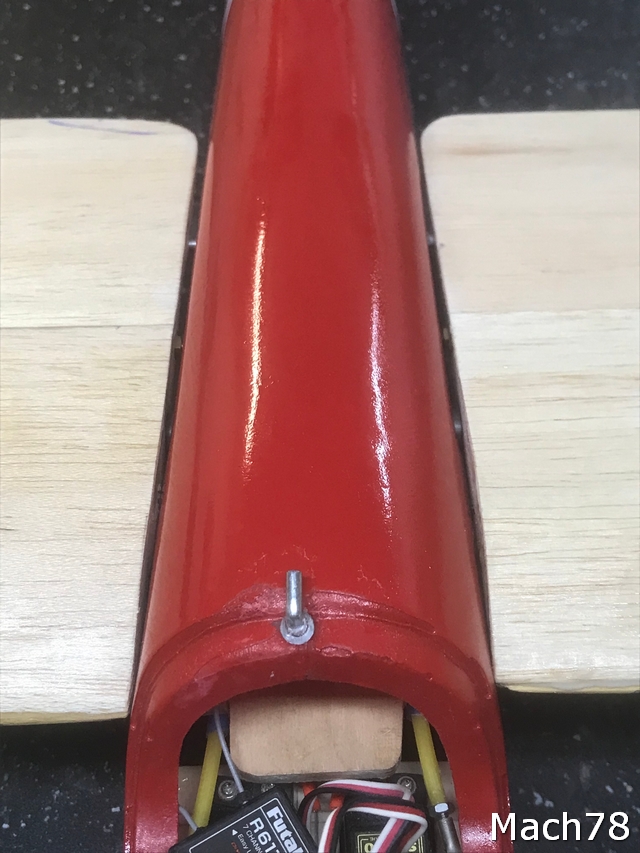
41/ On constate qu’il y a un léger défaut au raccord de karman à l’extrados de l’emplanture des ailes. Il faudra revoir ça avant l’entoilage.
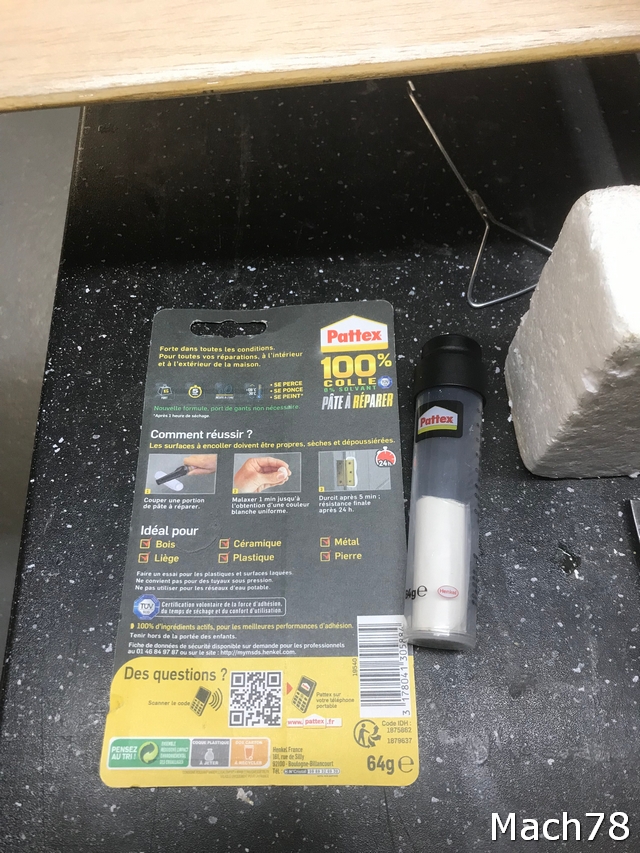
42/ Le mastic bi-composant utilisé pour faire la jointure aile-fuselage. Bien malaxer avant l’application en cordon entre les deux parties.
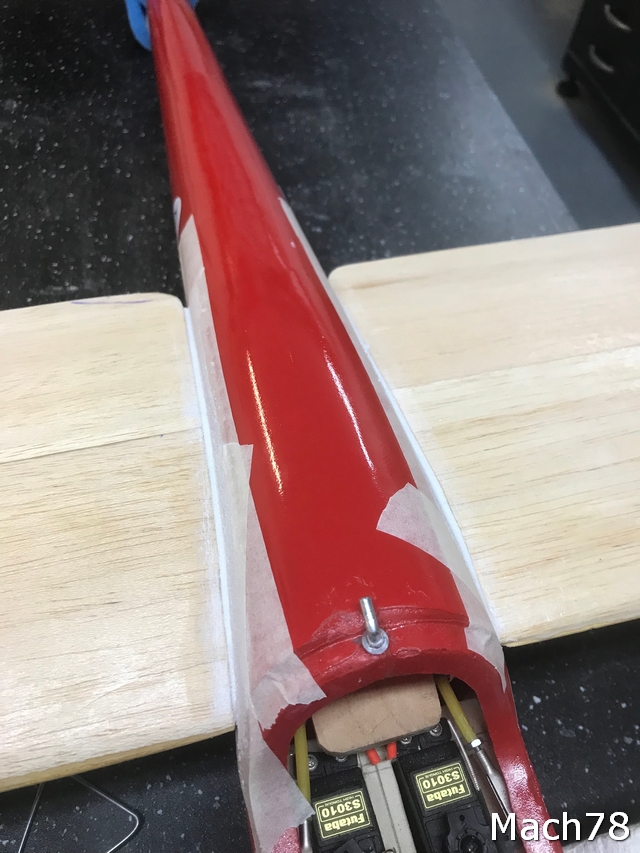
43/ Le scotch de peintre en place pour protéger et éviter toute adhérence sur le fuselage. On arrase avec un petit couteau à enduire. Attendre au moins 24 à 36 heures de séchage et de durcissement avant de poncer. Le raccord est impeccable, au moins visuellement.
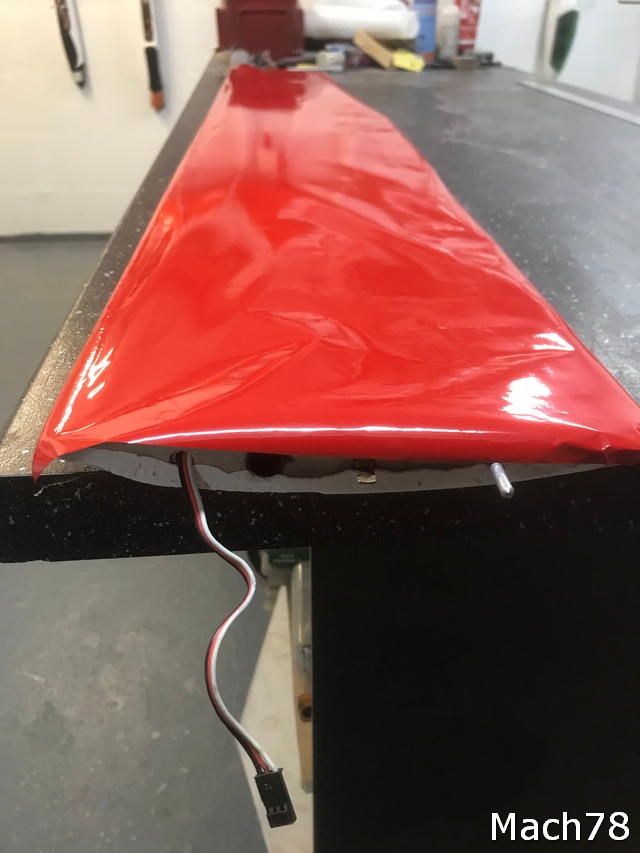
44/ Début de l’entoilage à l’ORACOVER. On commence par l’intrados, le morceau d’entoilage est délicatement posé dessus et ajusté avant la chauffe.
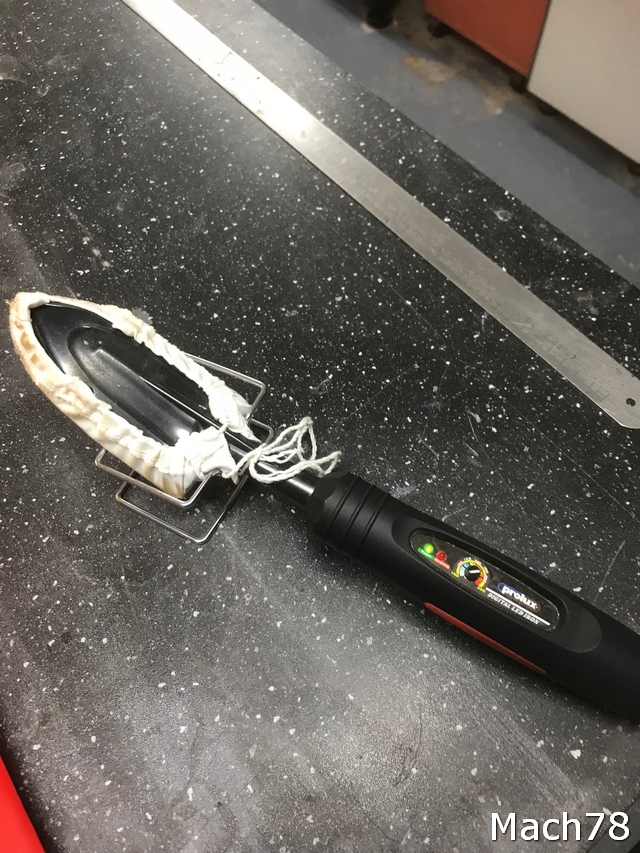
45/ L’outil qui va bien. La chaussette sur la pane du fer n’est pas indispensable mais évite de ‘rayer’ l’entoilage et permet une chauffe un peu plus élevée (+5°environ). Le thermostat sur le fer est incontournable lui.
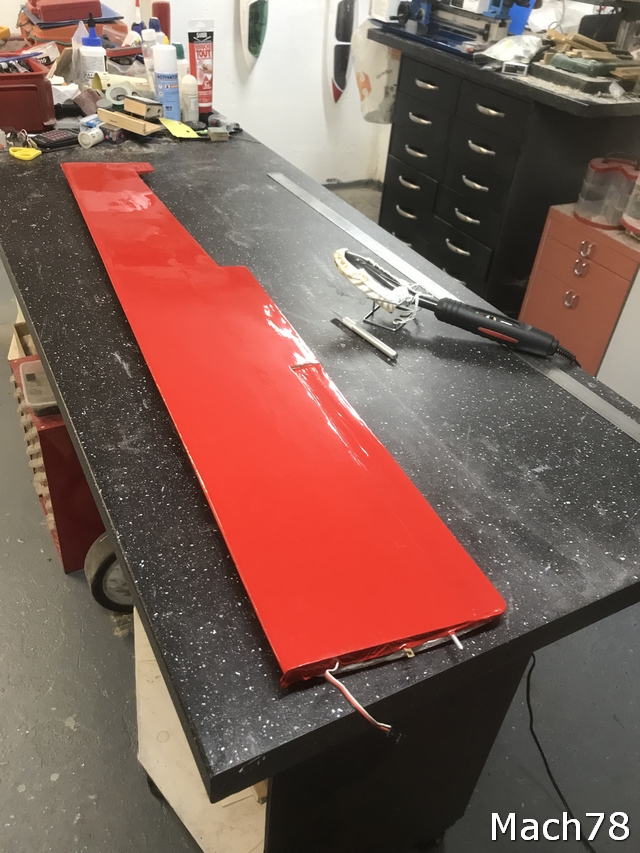
46/ L’intrados terminé. On chauffe à 180°-185° maximum. Au delà l’entoilage se perce et il faut recommencer toute l’opération avec un morceau d’entoilage neuf.
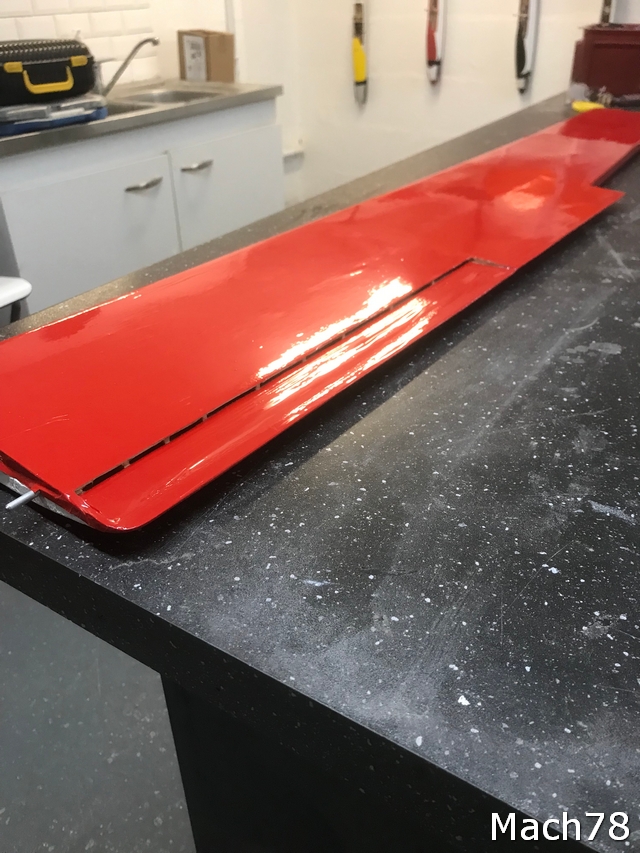
47/ Vue par le bord de fuite.
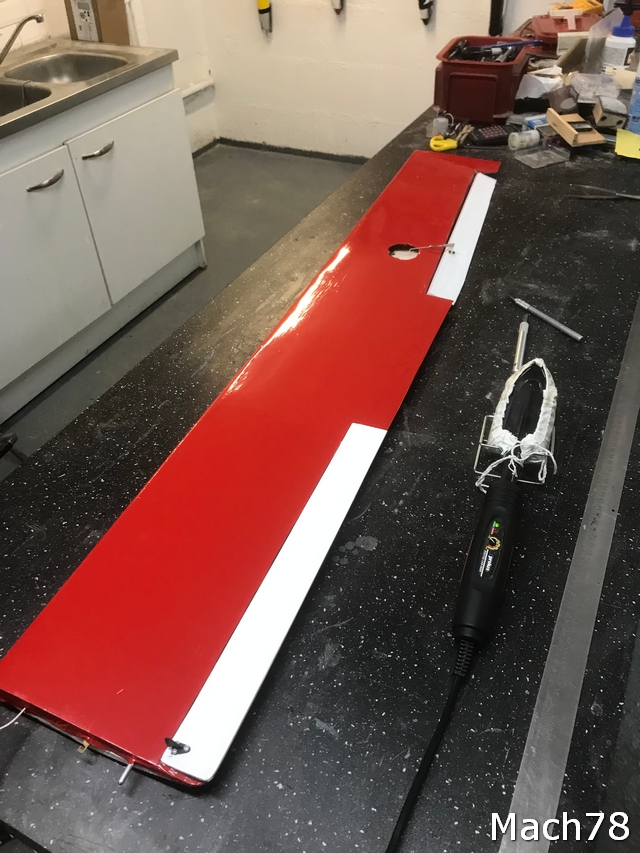
48/ Le volet de courbure et l’aileron présentés à blanc pour contrôler les jeux latéraux des gouvernes.

49/ Le puit du servo d’aileron dégagé. On aperçoit la prise de la ralonge du servo avec sa languette de verrouillage et le traçage de l’emplacement futur de celui-ci. Il sera collé avec précision à son emplacement avec du double face moussé.
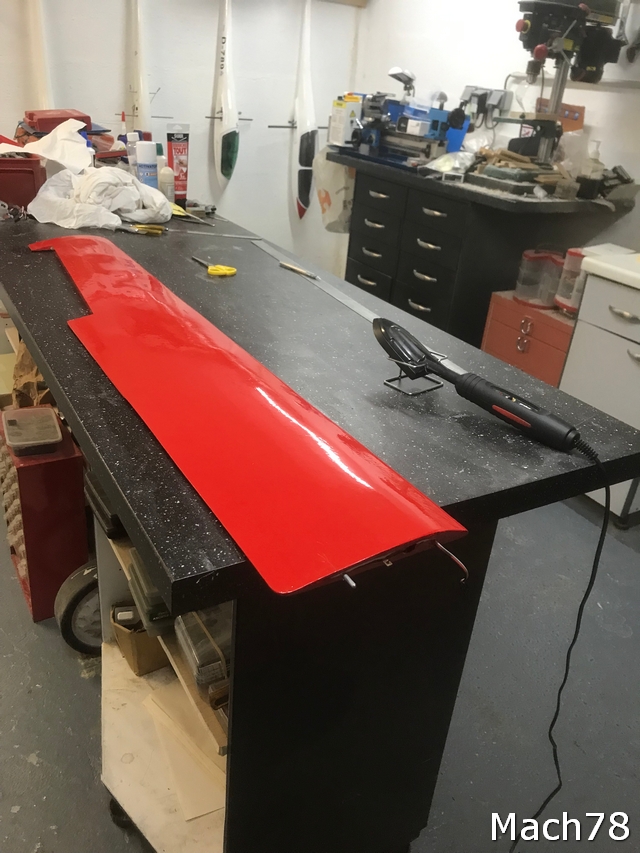
50/ L’extrados terminé. En étant précautionneux, il faut compter environ une demie heure de travail total par aile.
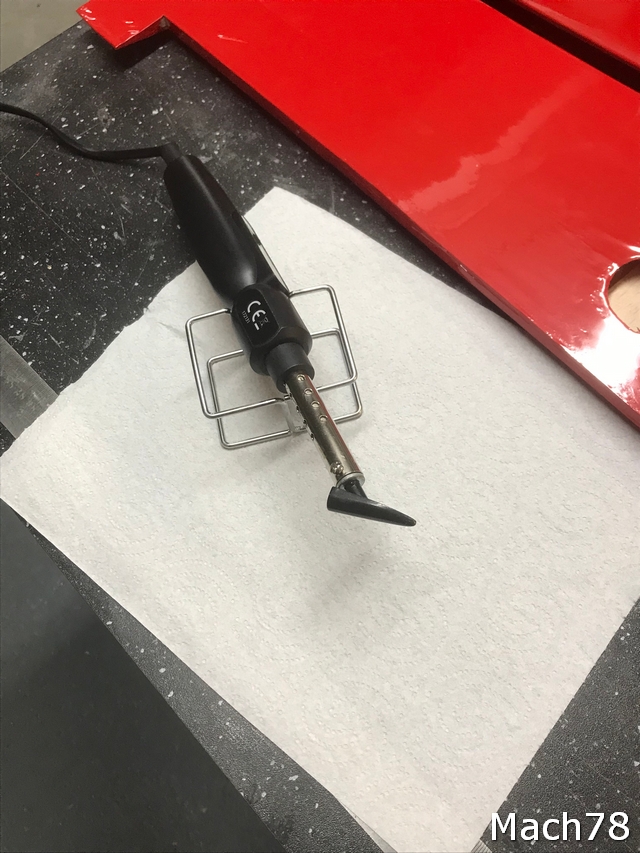
51/ Le petit fer à entoiler du club, très pratique. Sa pane est courbe et permet de rabattre facilement l’ORACOVER dans le puit du servo.
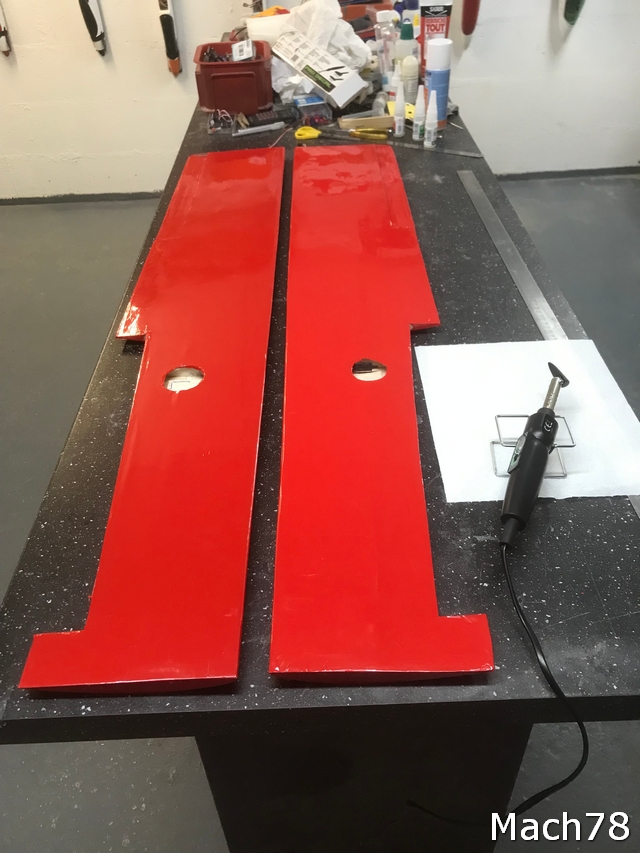
52/ Les ailes entièrement entoilées intrados-extrados, les puits de servo finis.
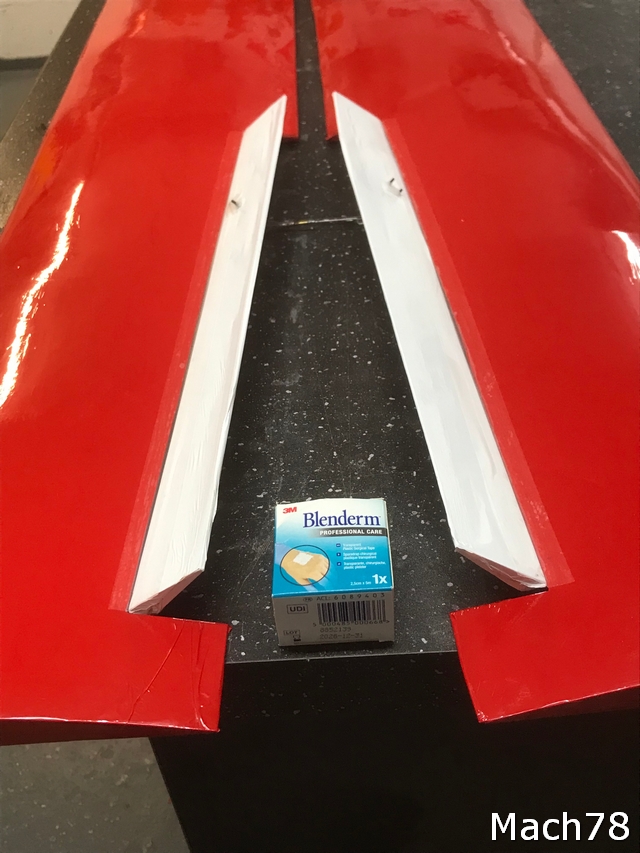
53/ Mise place des ailerons. Ceux-ci sont fixés avec du ruban adhésif médical BLENDERM. On peut le remplacer par du scotch CRYSTAL moins cher et plus facile à utiliser mais bien moins résistant aux ultraviolets. Les débattements sont exagérés pour s’assurer du bon fonctionnement. Les tringles de transmission des servos ne sont pas encore en place.
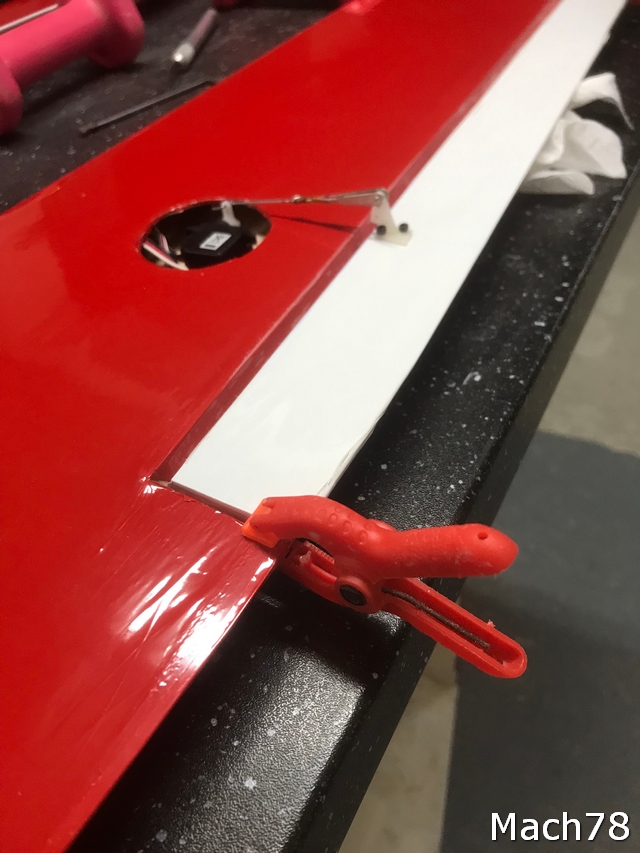
54/ Une pince pour maintenir la gouverne au neutre puis on règle la transmission pour que celle-ci respecte le neutre du servo. Les réglages affinés se feront via les sous-trims de la radio-commande.
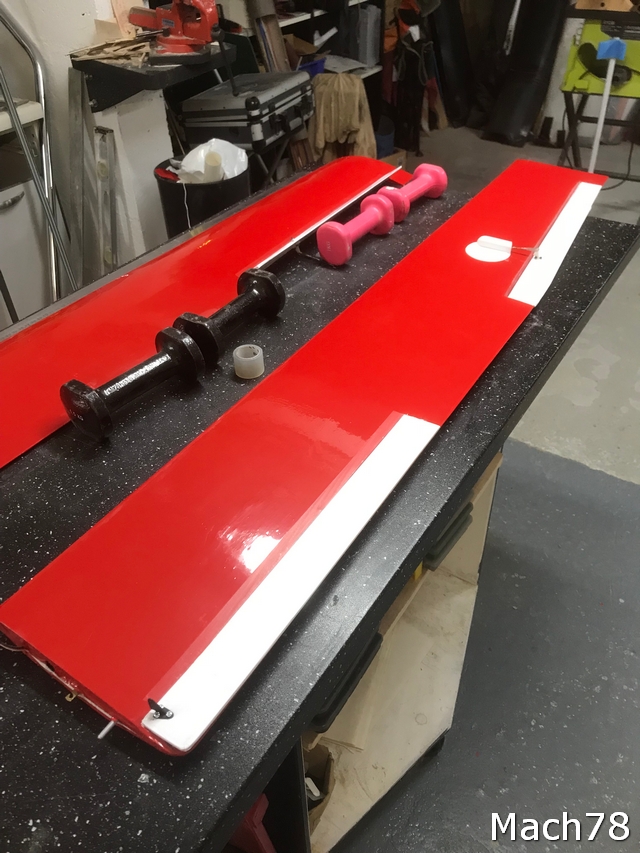
55/ Le volet de courbure et le capot de servo en place.
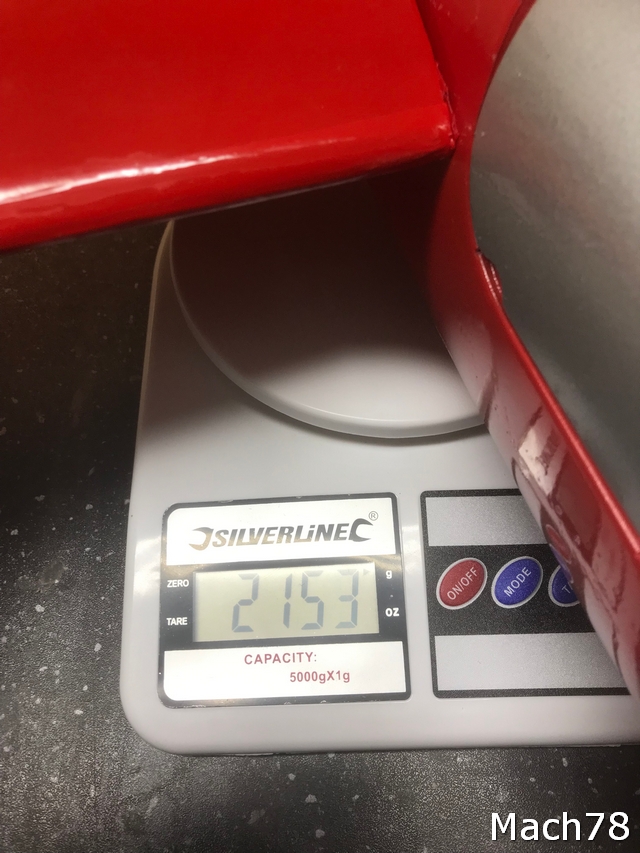
56/ Le poids de la bête en ordre de vol.
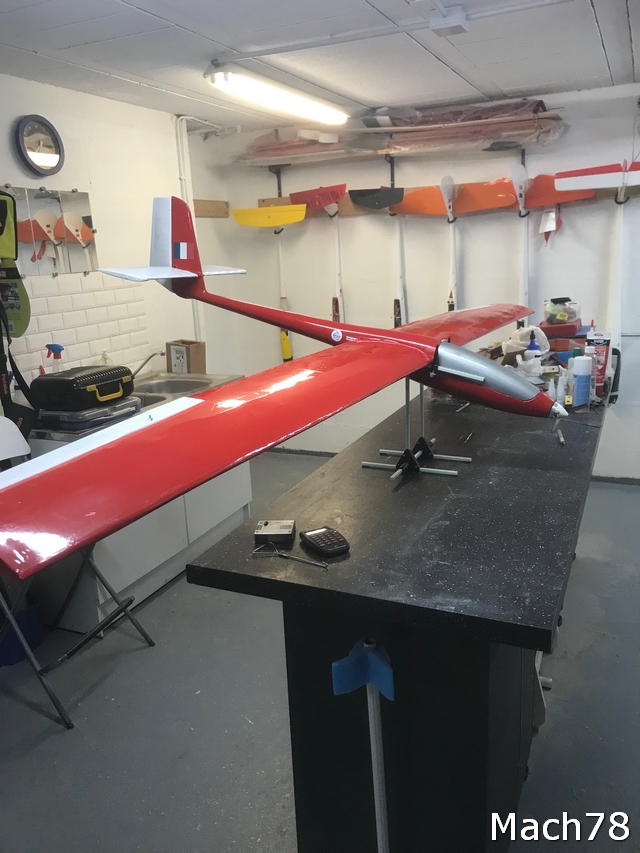
57/ Le REDFLAG avec son accu LiPo de 2200mA au centrage sur la balance aéro-dynamique, il est centré beaucoup trop avant … Mais ça c’était prévu.
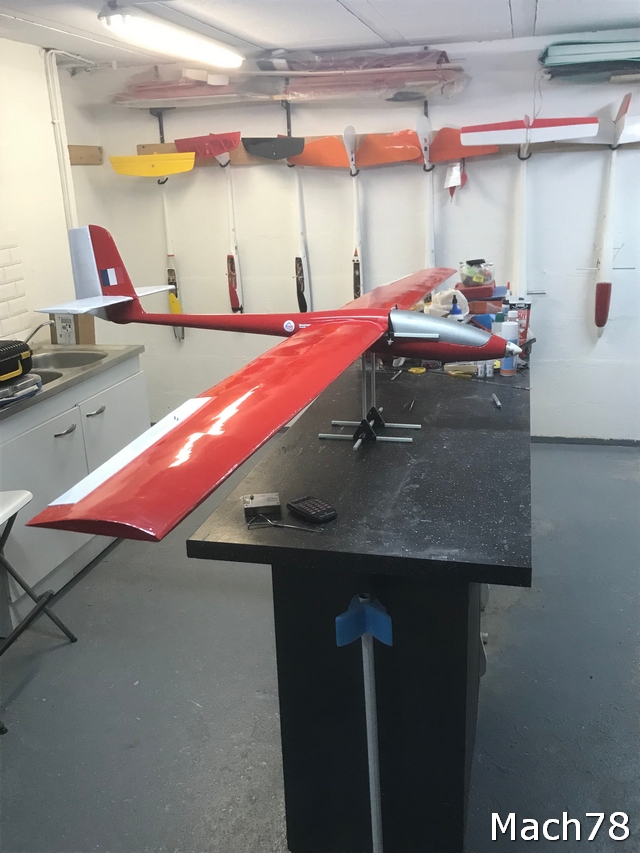
58/ Avec 28g de plomb dans la dérive, le centre de gravité est conforme aux calculs.
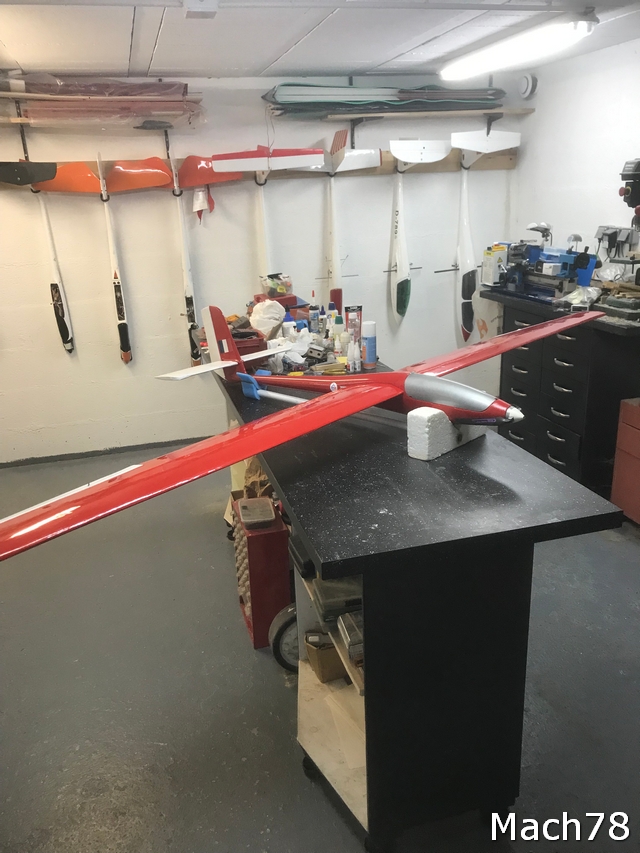
59/ Voilà, le REDFLAG est terminé. Il ne reste plus qu’à planifier la première mise en altitude lors des beaux jours avec notre pilote d’essais Alexandre.